Row extraction lines
Typical feeding system for horizontal flowpack machines in chocolate, snack and bar packaging lines.
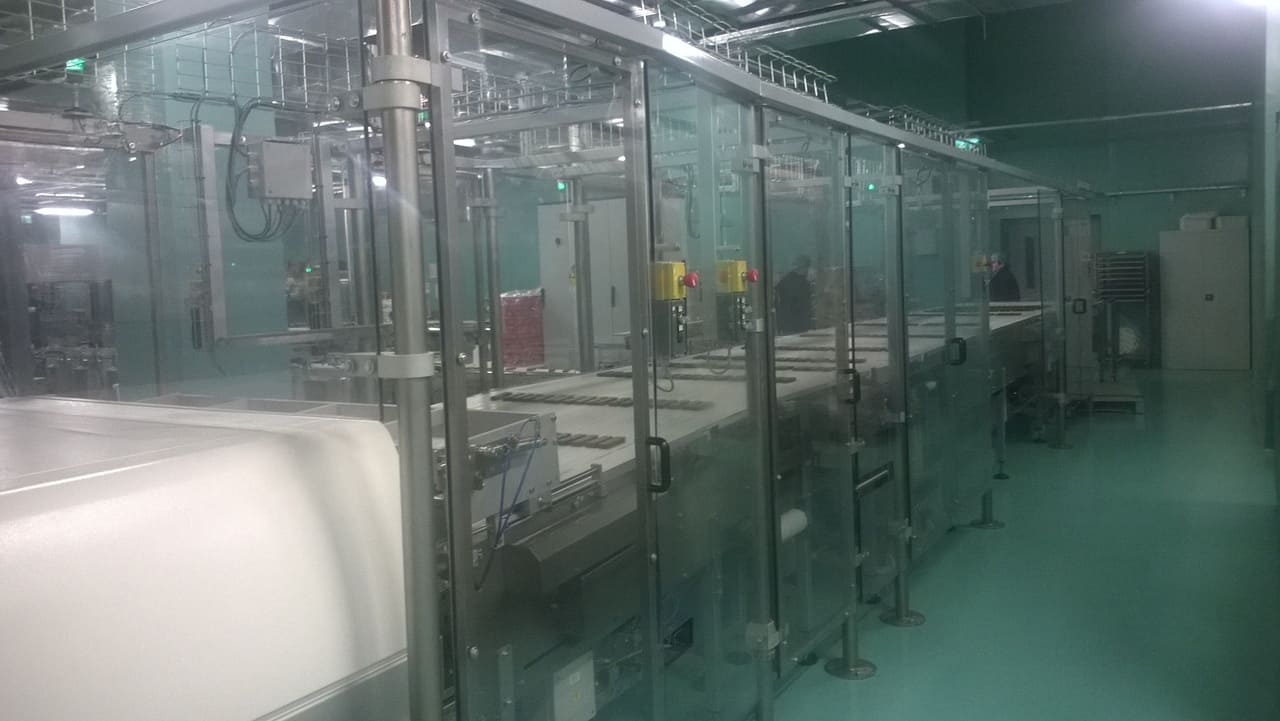
Technical features:
AISI 304 or mixed structures with anodised aluminium.
Cantilevered version available for quick belt change.
Available widths from 600 up to 1600 mm.
Pneumatic or brushless drives.
Row lines are horizontal packaging machine feeding systems suitable for chocolate bars, snacks, cereal bars and sponge cakes. These lines are positioned at the outlet of ovens, process lines or modellers, they are made in modules to adapt to different requirements to feed one machine or multiple machines by managing the flow.
All lines are composed of belt conveyors equipped with scrapers to clean the belt from food residues with collection trays for cleaning and automatic skid control systems. Depending on the requirements, it is possible to realise the structures in sheet metal or with a combination of AISI 304 sheet metal and anodised aluminium plates in order to obtain a cantilevered configuration that allows rapid extraction of the belts to facilitate maintenance.
Available Modules
- Alignment station: Consisting of a belt with a pneumatically or brushless driven levelling bar (above 60 ranks/min). Used to correct the alignment of incoming products, ensuring a uniform arrangement along the packaging line.
- Bypass and Product Rejection Systems: Designed with an oscillating or retractable head, these systems are pneumatically driven and can discharge the product into a reject belt or bypass line. These stations can be integrated in the alignment module or in a metal detector.
- Packaging machine feeding: The feeding stations to the packaging machines consist of a belt conveyor with an oscillating header and a transverse rip-off belt. Faster lines or lines with more delicate products can also have an intermediate holding and launching belt between the bascule and the extraction belt, and the latter can be mounted on a trolley to retract at the same time as the products are received. This system is particularly useful when dealing with fragile and deformable products such as covered sponge cakes and cereal bars.
- Gap closing belts: Placed after the extraction belt and in a variable number depending on the line speed, their purpose is to ensure that the flowpack is fed as continuously as possible.
- Bar rotation: After the gap closing , for rectangular products, there is a double belt system that rotates incoming products by 90° in order to supply the flowpack with products on the narrow side.
- Quality control: Consisting of a conveyor and a motorised ploughshare with adjustable inclination change, its purpose is to centre the product with the inlet of the machine and to reject products that have not been correctly processed by the turner, in order to avoid jamming.
- Accumulation: In addition to our multi-platen FIFO system, which can be perfectly integrated into the lines and which you can find in the dedicated section of the site, it is also possible to insert a LIFO system at the end of the line with production recovery only on the last packaging machine. Although less flexible, this is a more economical solution and particularly suitable for lines with multiple machines.
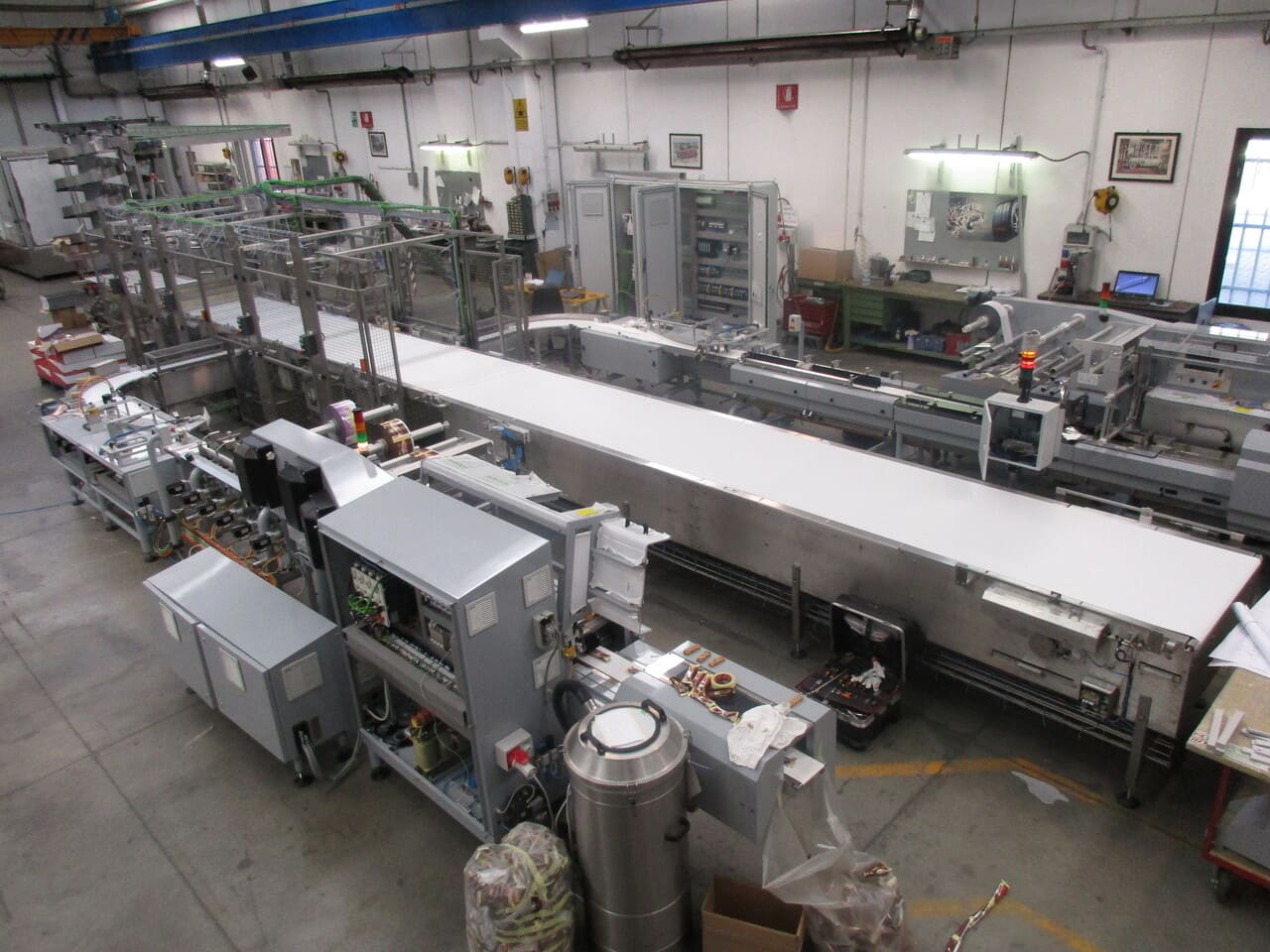
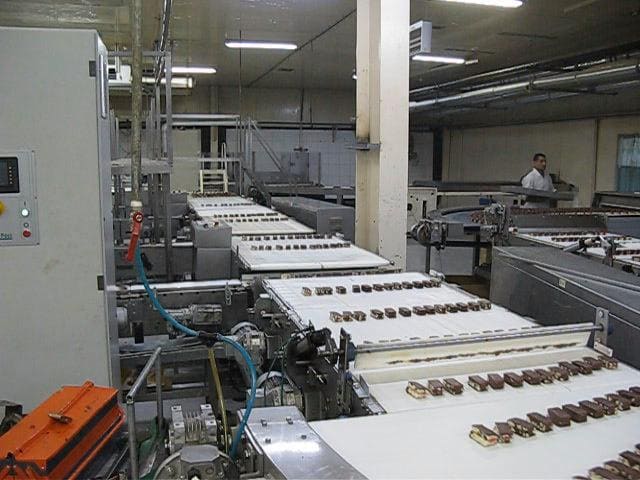
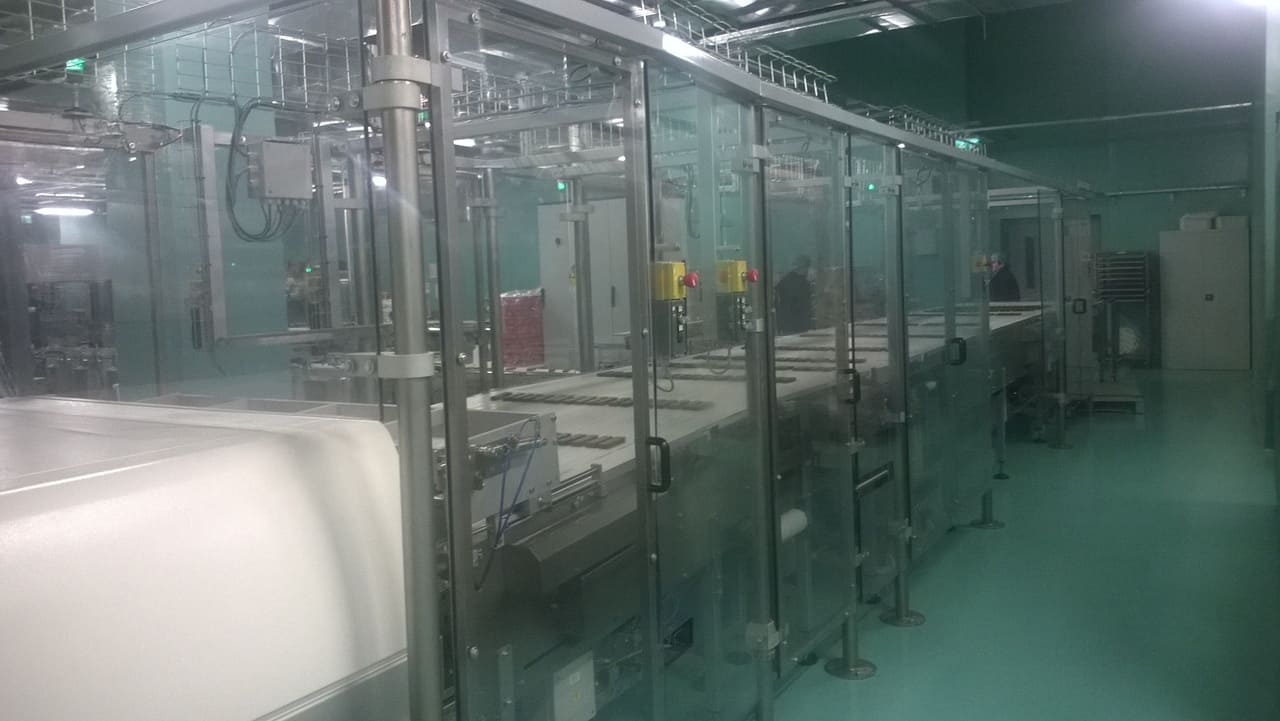
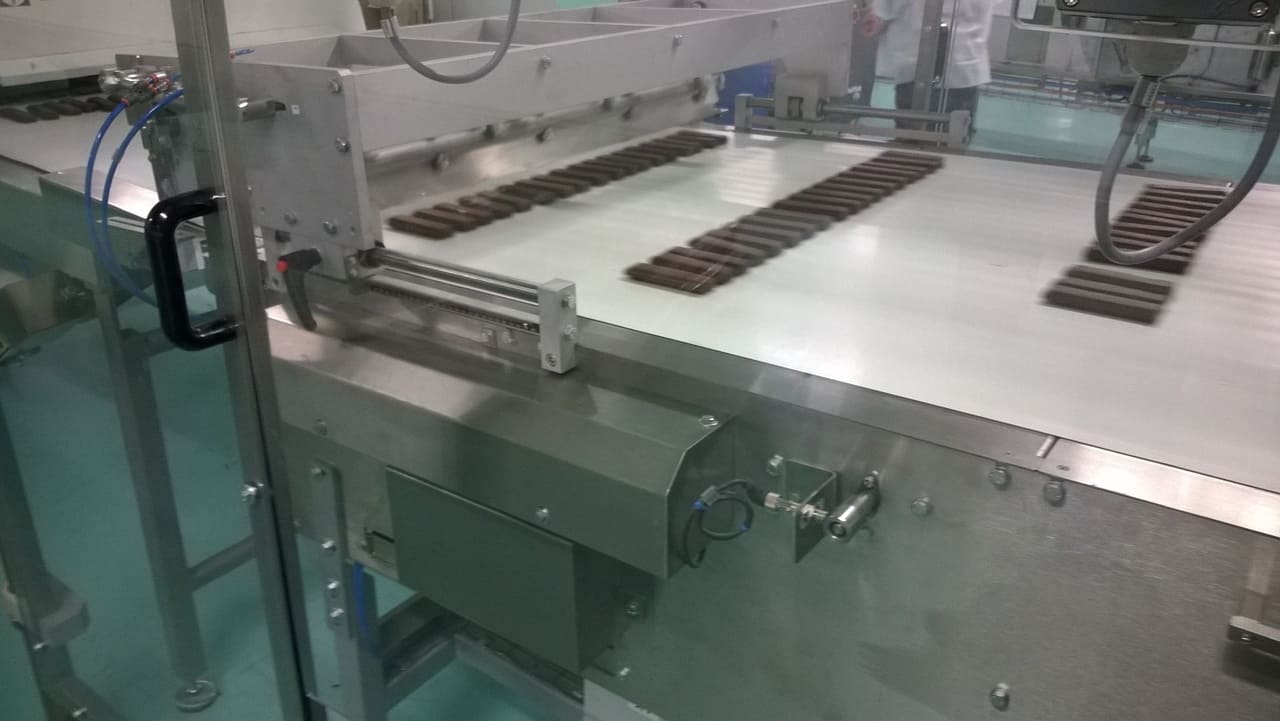
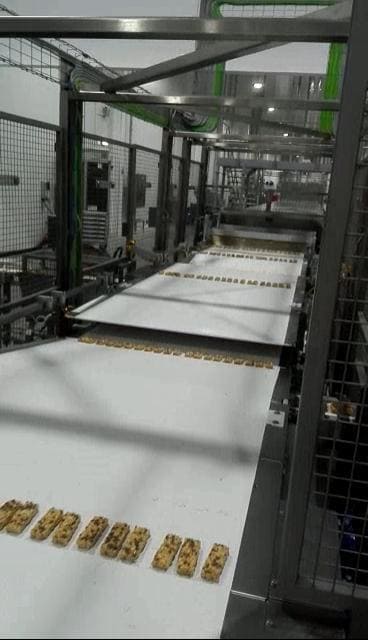
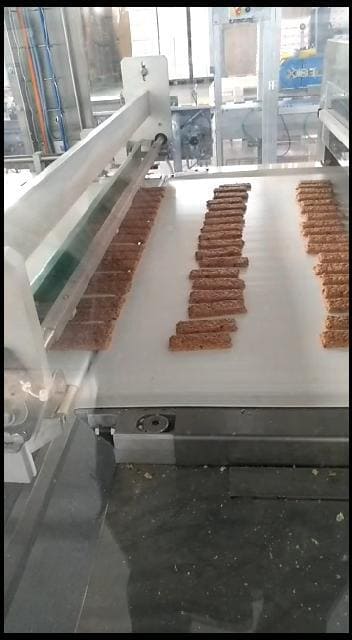
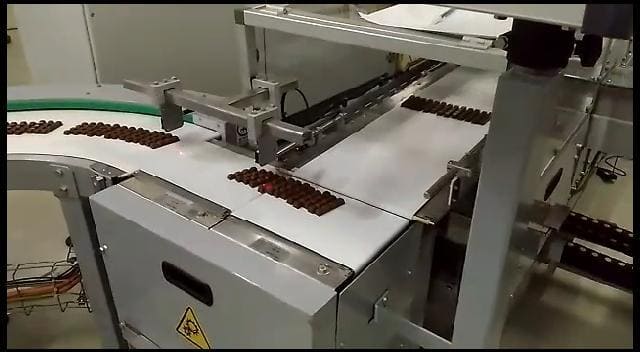
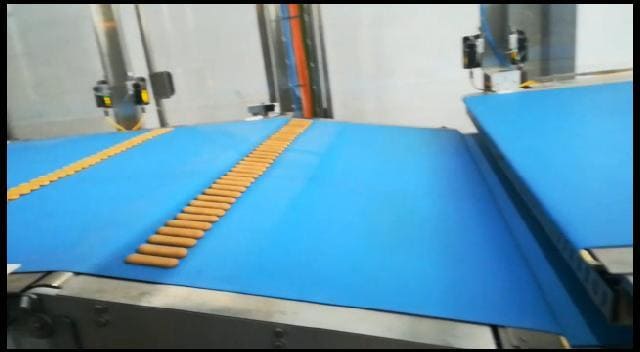
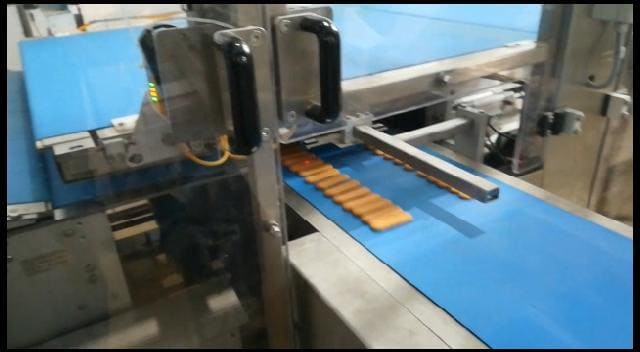
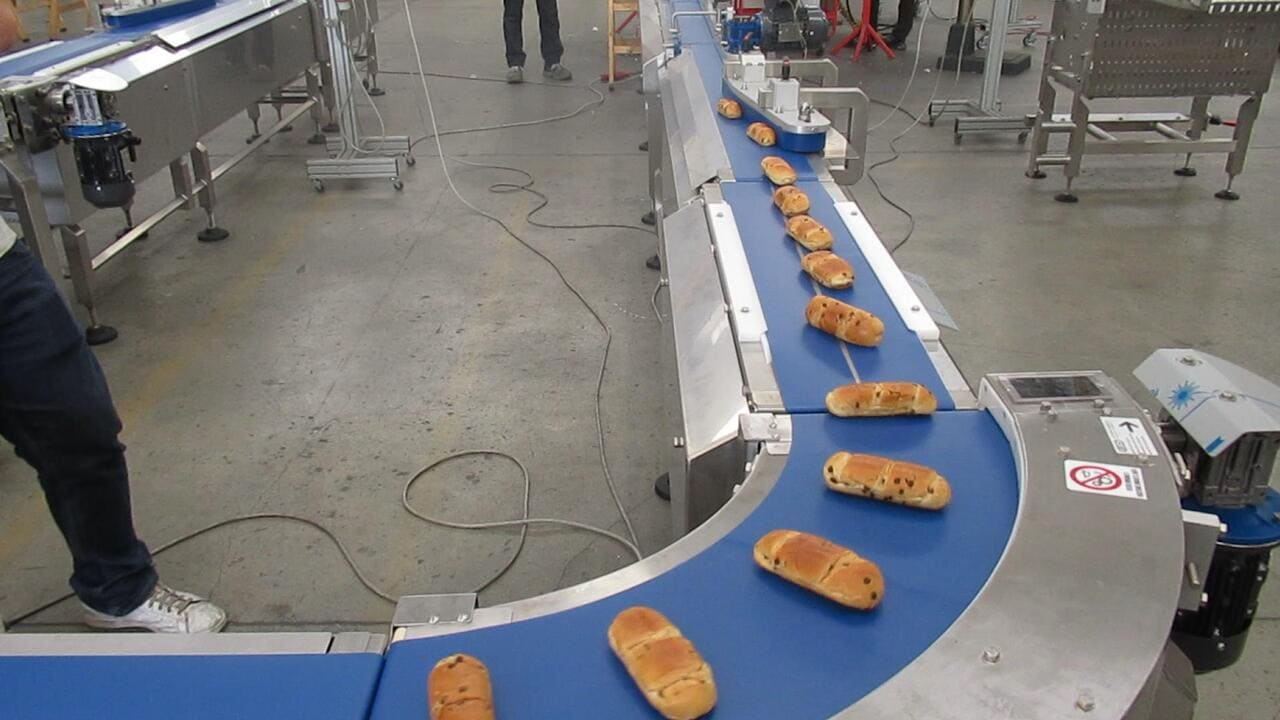