Pater Noster
Vertical shelf storage system with LIFO operating logic, suitable for plants with limited floor space.
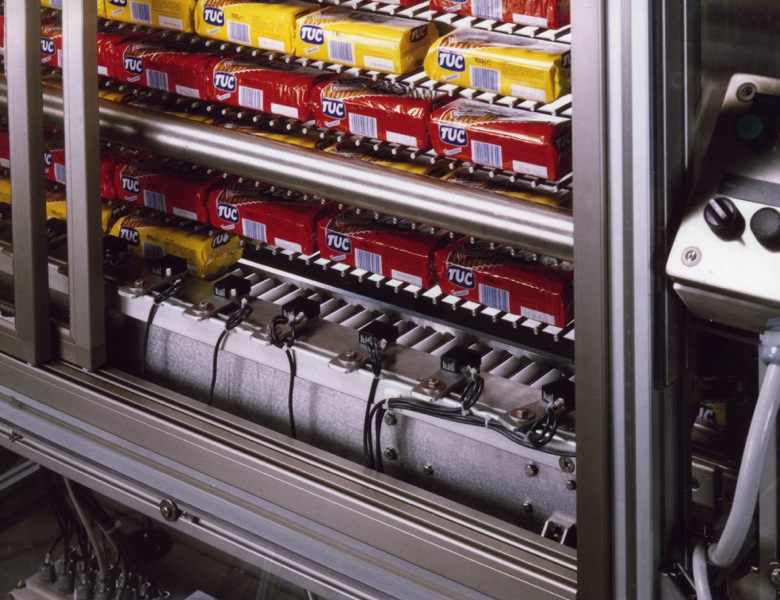
Technical features:
- Floor space: 1 metre wide, 3 to 5 metres long
- Height: 2.5 to 5 metres
- Frame material: anodised aluminium or AISI 304
- Belt width: Variable
- Accumulation: 10 to 50 metres
- Productivity: 50-150 ppm
The Pater Noster is one of the 'oldest' accumulation systems in the world of industrial automation, and although it is now surpassed in speed and flexibility by spiral solutions, it retains a niche of applications where it is a winner.
The main advantage of the Pater Noster is that it only develops longitudinally and in height, maintaining a narrow and long footprint, which is often required in older factories where there are multiple packaging lines. The prerequisite for a Pater Noster is that the products handled in the line can accumulate, withstanding a certain degree of reciprocal pressure. The machine consists of three sections: an infeed belt, a shelf elevator, which forms the main part of the machine, and finally an evacuation master. Normally, both the infeed and evacuation belts should be at least as long as the accumulation shelf.
During normal line operation, the products pass through all the belts of the line, at twice the nominal speed, without stopping. In the event of a downstream stop, a pneumatic cylinder stops the products inside the shelf elevator and starts accumulating them. When the shelf is completely full, a second pneumatic stop stops the incoming products and begins to accumulate them on the infeed belt, giving the system time to lift the shelf one step and provide a new free shelf for further accumulation. At this point the stop on the infeed conveyor is released and the loading cycle starts again, possibly until it is completely full.
When the downstream line restarts, the system begins the unloading cycle. A well-designed line will have downstream machines that allow the accumulated production to be recovered without necessarily having to stop upstream, they must therefore be able to handle at least 10% of surplus production. The unloading cycle, during normal production, involves stopping on the infeed belt to block accumulated products. When the crossing belt is free the elevator descends one step, placing all the products stored on it and letting them go to the next packaging machine, at which point the stop on the infeed belt can be released. Depending on the overcapacity of the downstream line, this cycle can be performed once or several times a minute, gradually emptying the buffer, which will obviously operate with LIFO logic.
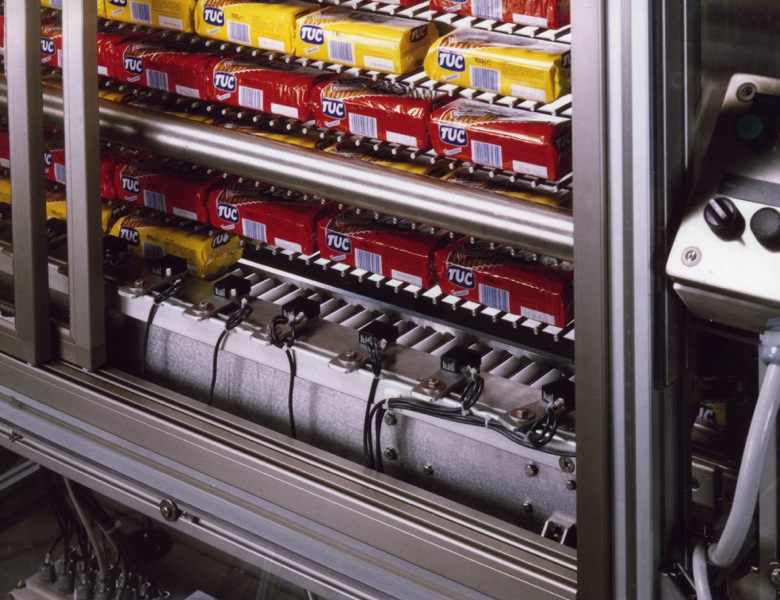
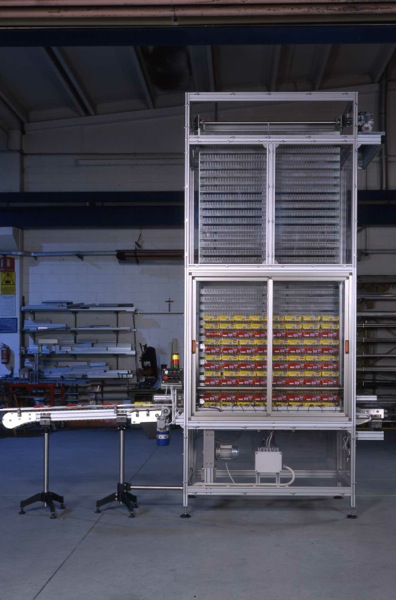
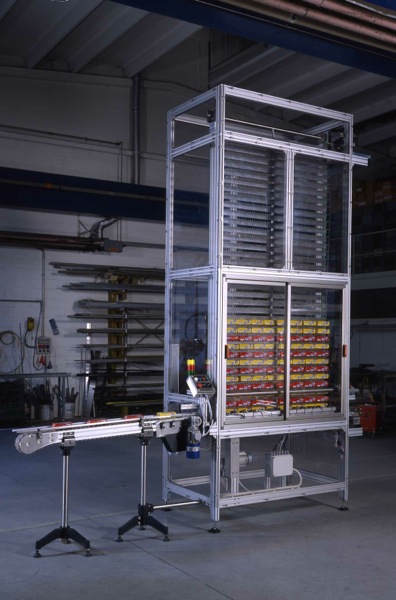
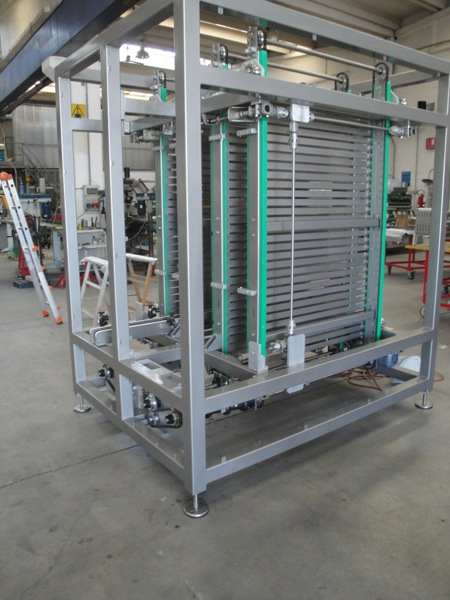
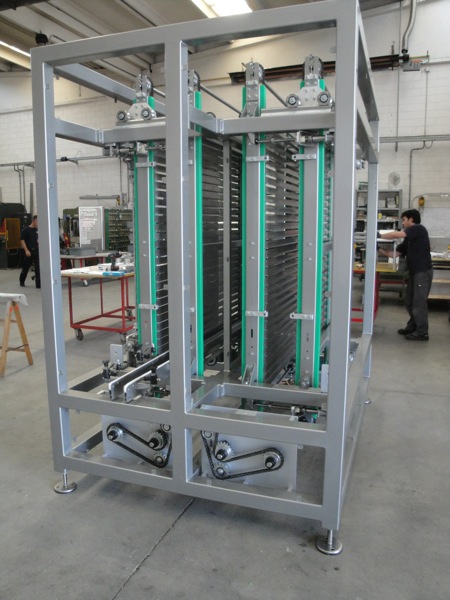
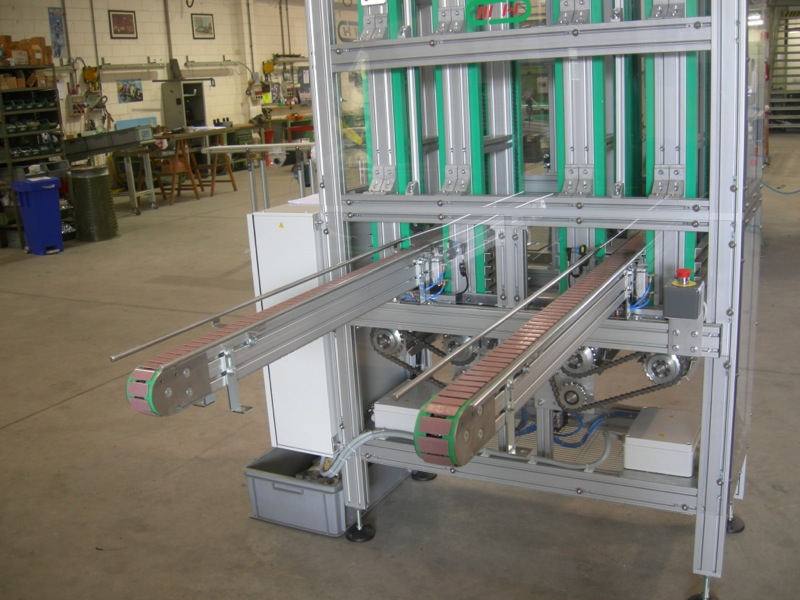
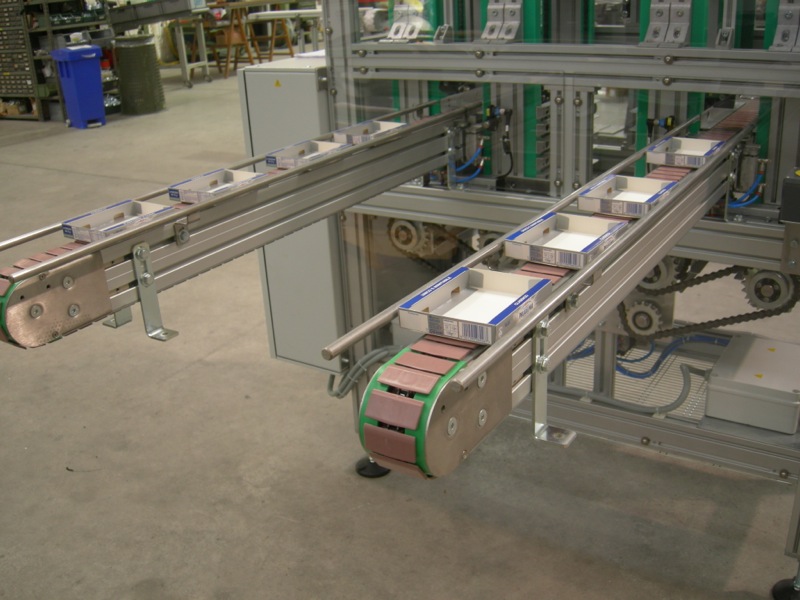
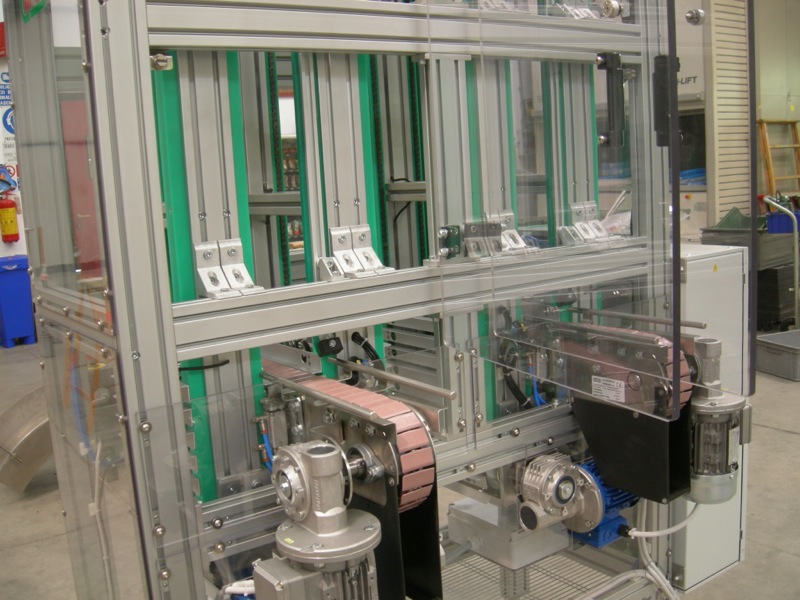
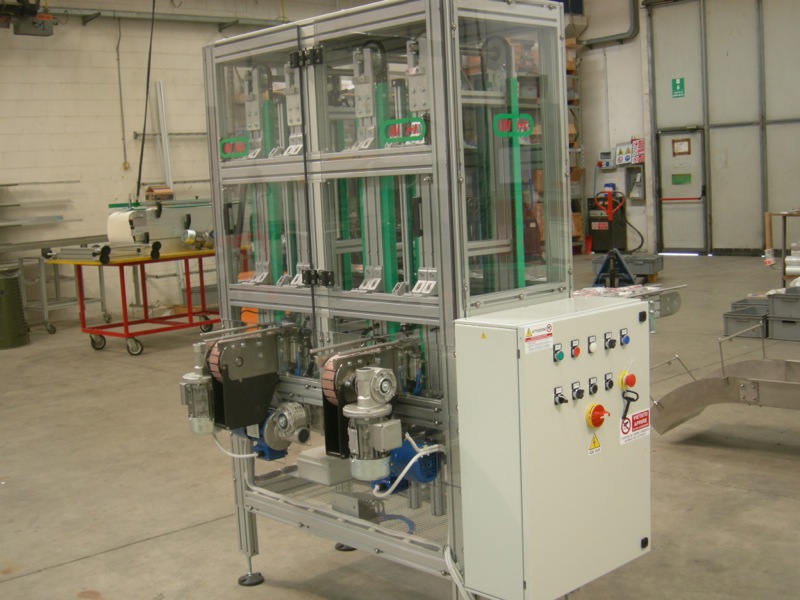
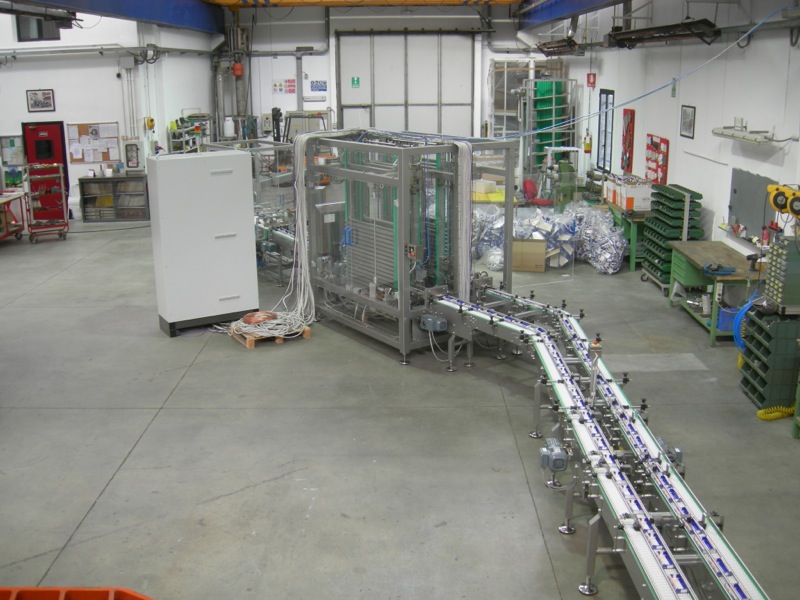
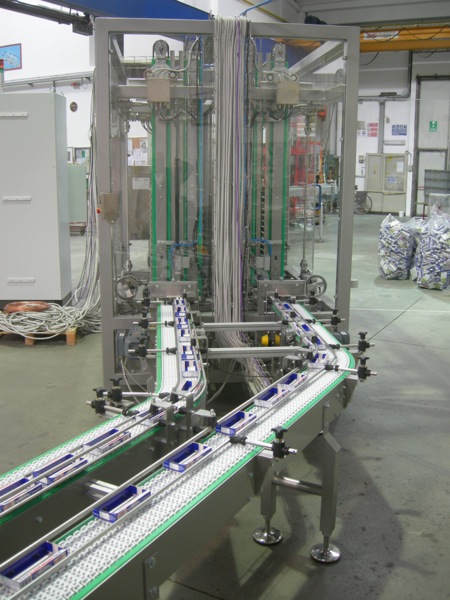
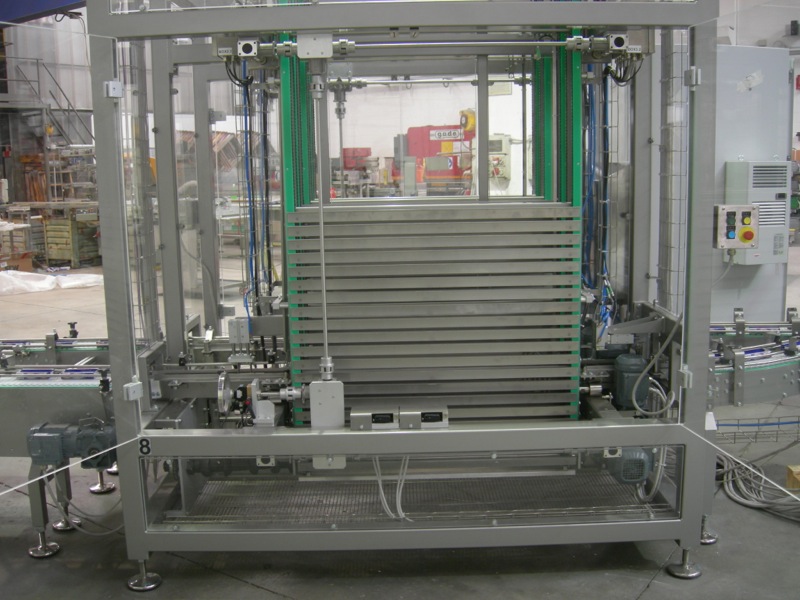

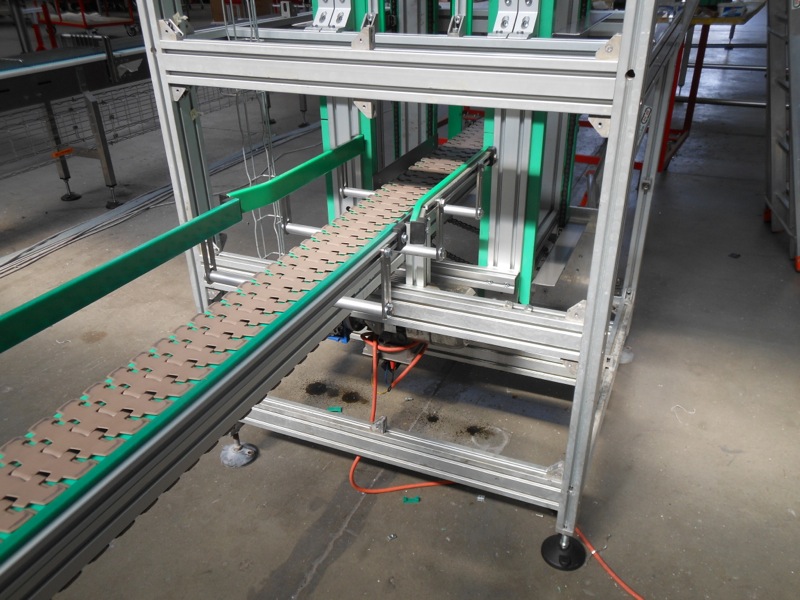
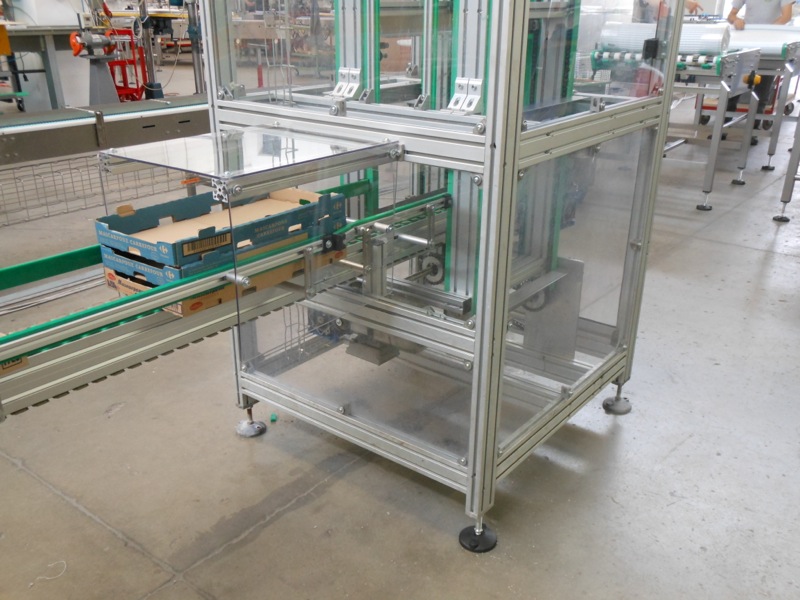
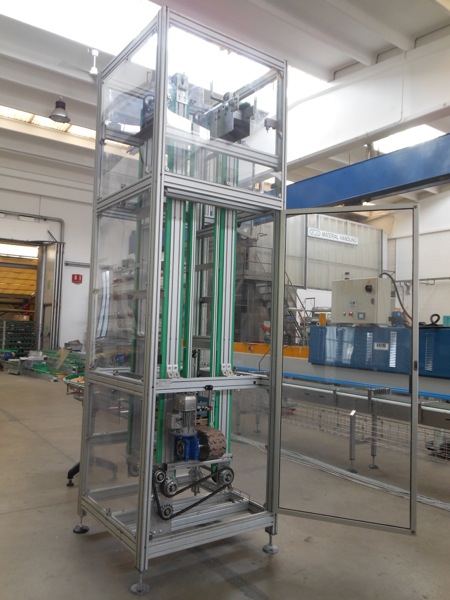
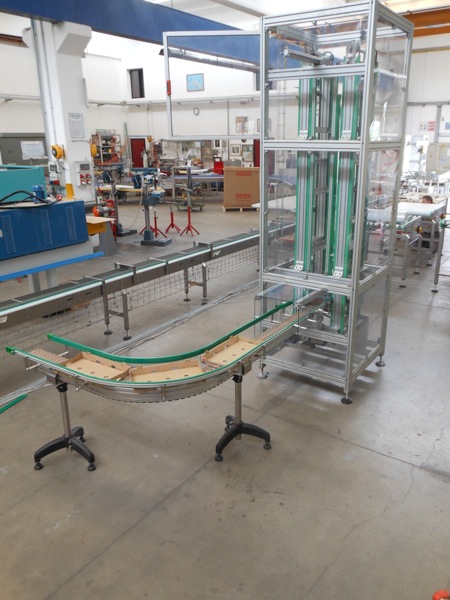
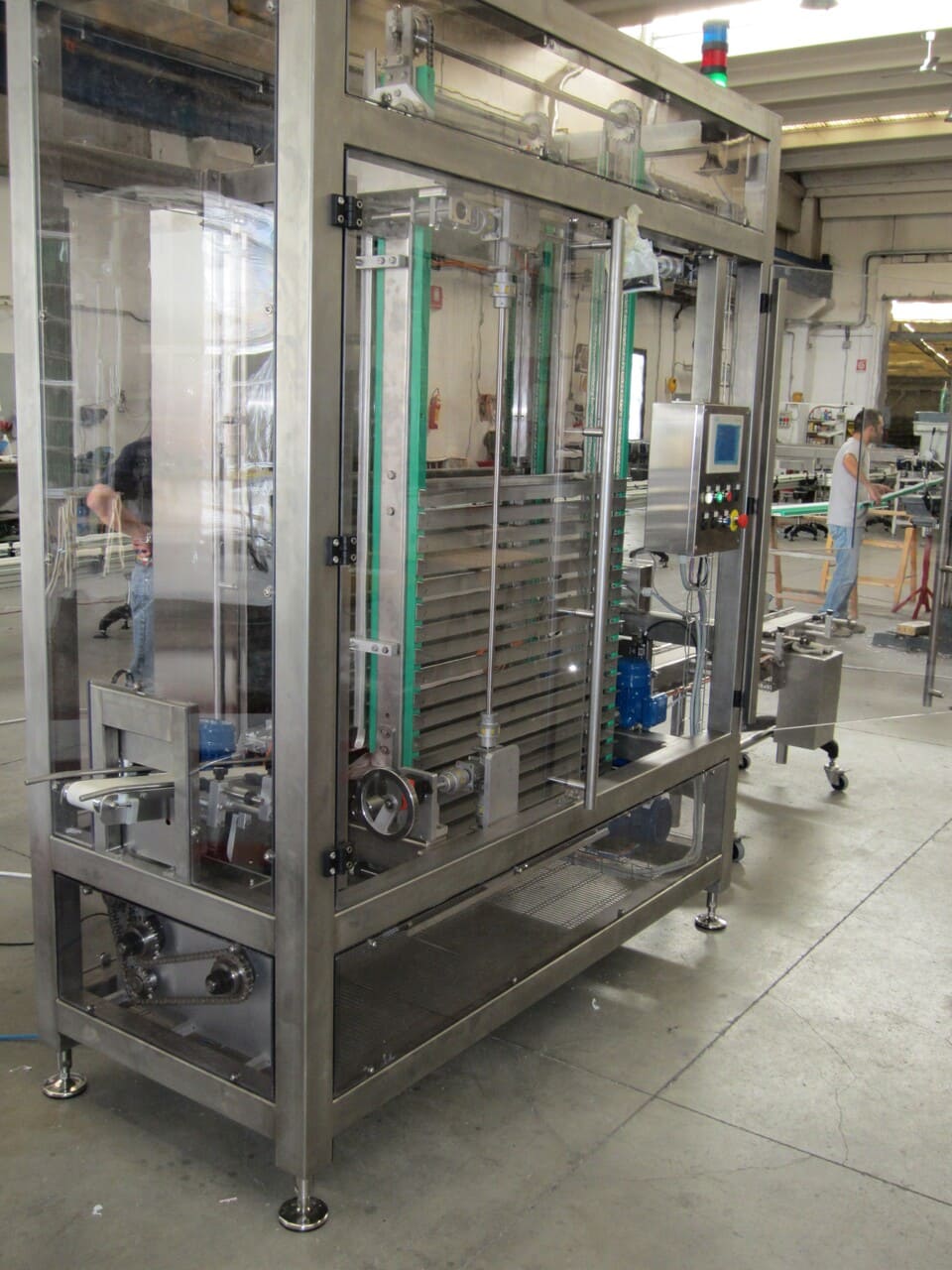
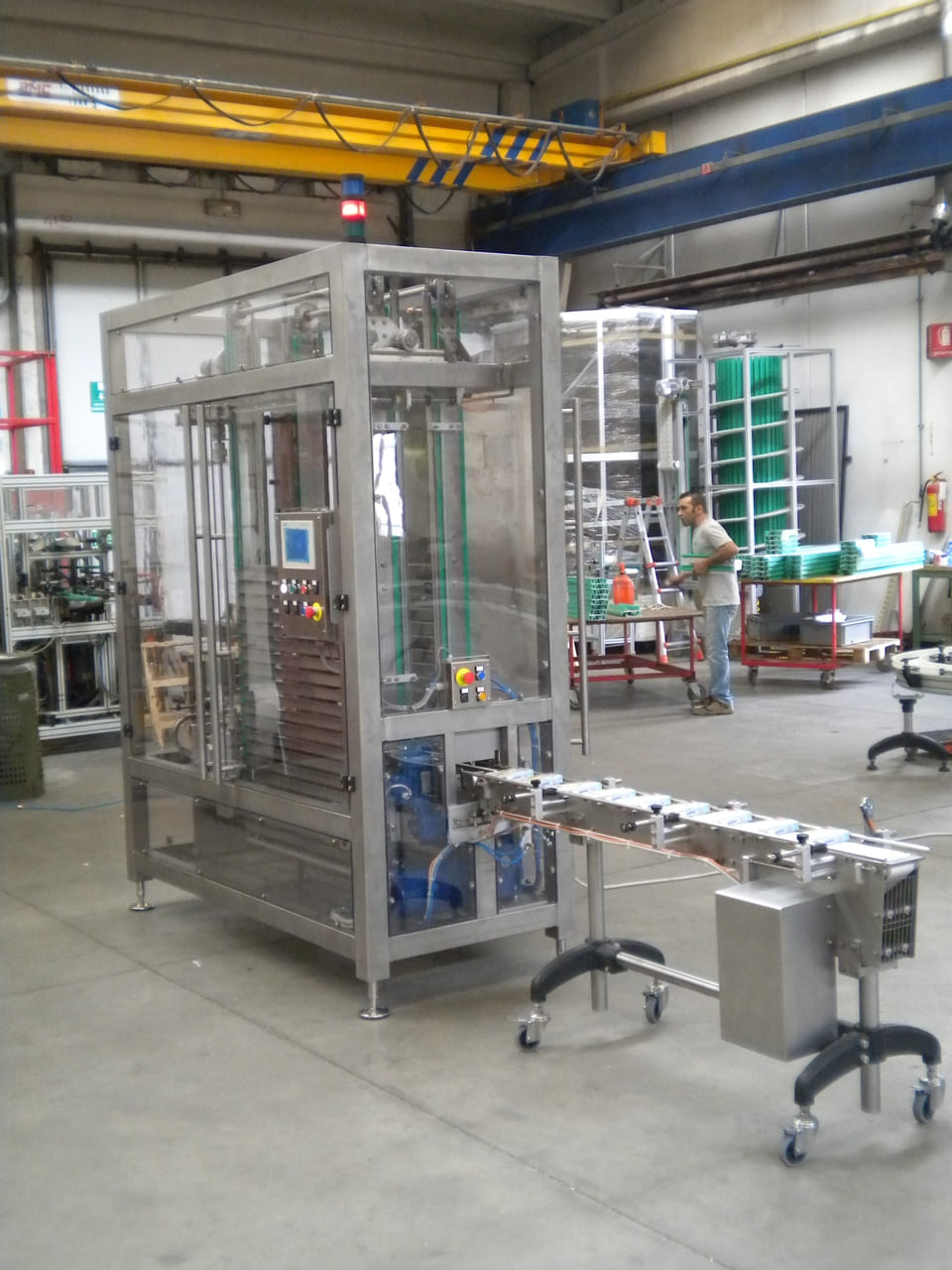
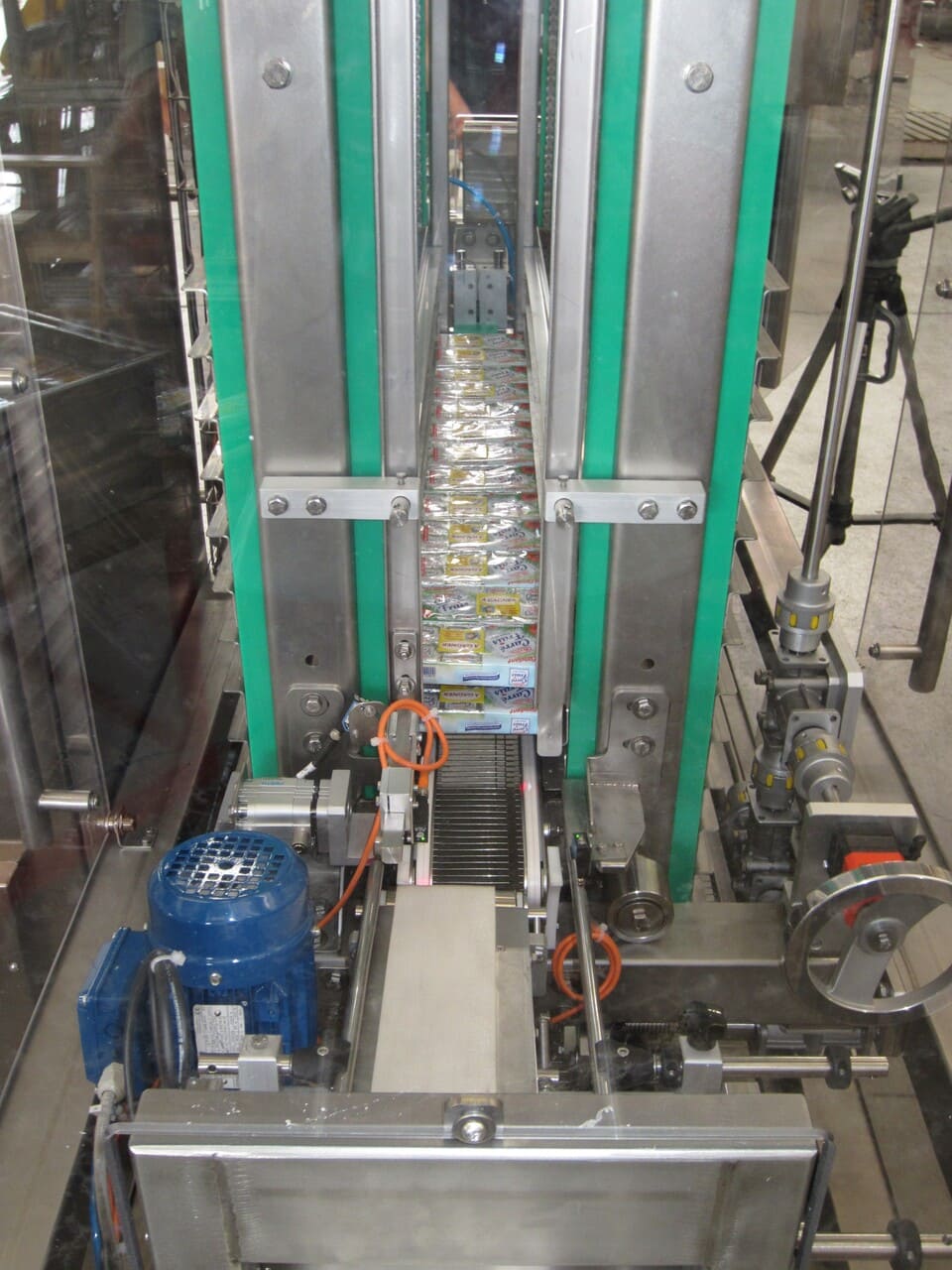