The preparation of meat and sausages at an industrial level is a very particular niche that is divided into two distinctly different phases, both in terms of operations and timing.
The actual preparation phase (slaughtering, boning and preparation of the cuts) ends either with the immediate passage to the packaging department or, much more often, to some form of preservation and seasoning of the large cut in cold storage. Once this stage is complete, the product can be shipped directly to the counter or further processed to obtain shelf-stable portions.
The preparation and processing phase still involves a lot of manual work, at least to obtain the large cuts. Depending on the desired production, products are either allocated to SKUs, usually reusable plastic crates of 400x600 mm size for transfer to cold storage or proceed directly to specialised machinery such as meat mincers, slicers and portioning machines.
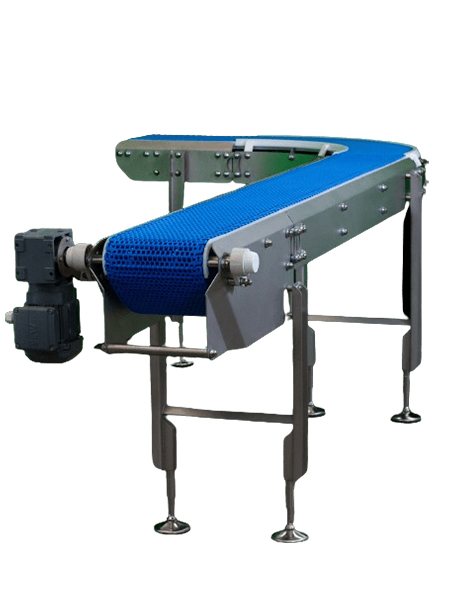
Sani flex
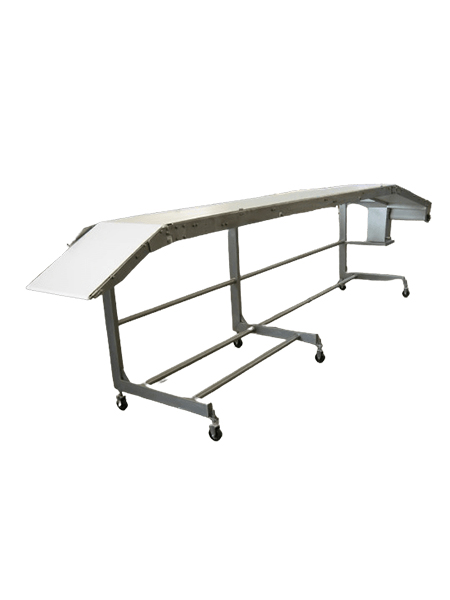
Washable belts
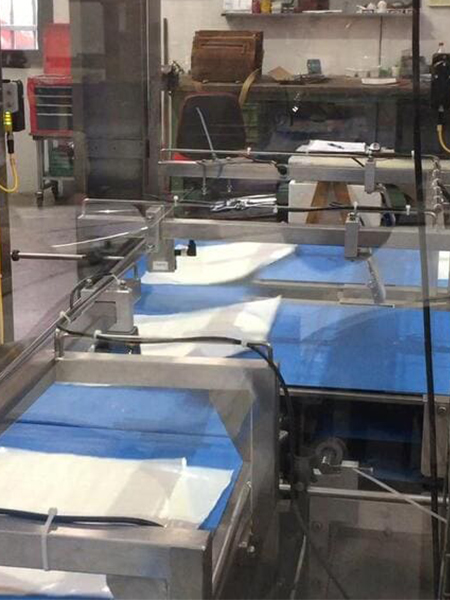
Retractable Conveyors
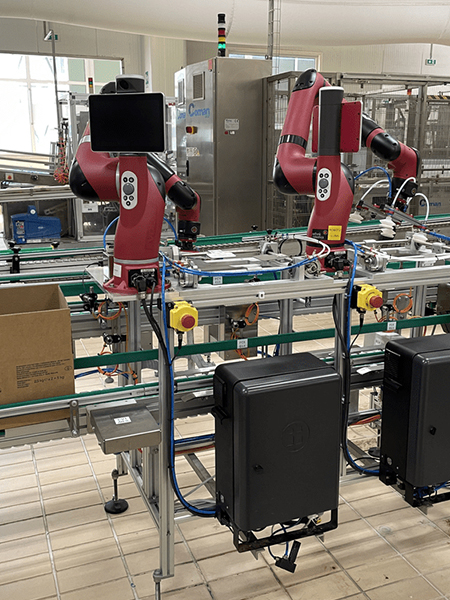
Cobot feeders
When working with pre-printed trays, there may be some transport between the filling machine and the sealing or cellophaning of the pack.
In this case the product is no longer in direct contact with the conveyor belts, so a run of washable conveyors may be sufficient; however, it is not uncommon for companies to protect themselves by continuing to use the hygienic standard at least until the pack is completely sealed.
Denesters for empty trays, pull nose loaders and robotic filling systems are among the accessories that can be added to the lines.
Sani flex Washable belts Retractable Conveyors Cobot feeders
Thermoforming machines
Thermosealing machines
Primary packaging machines, typically thermoforming or heat sealing machines, are used for packaging foam or preformed plastic trays. There are different versions of these machines: while thermoforming machines practically always have a multi-row output, traysealers can also come in a single-row configuration. In any case, these are machines with intermittent operation.
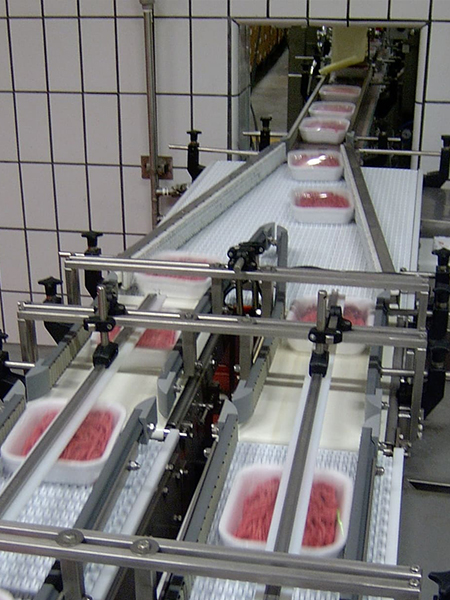
Mergers
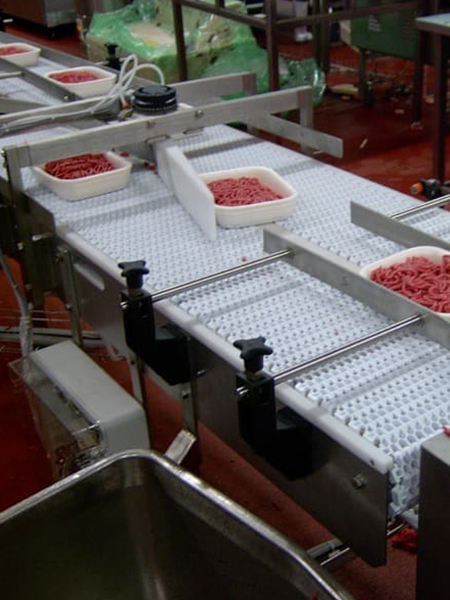
Dividers
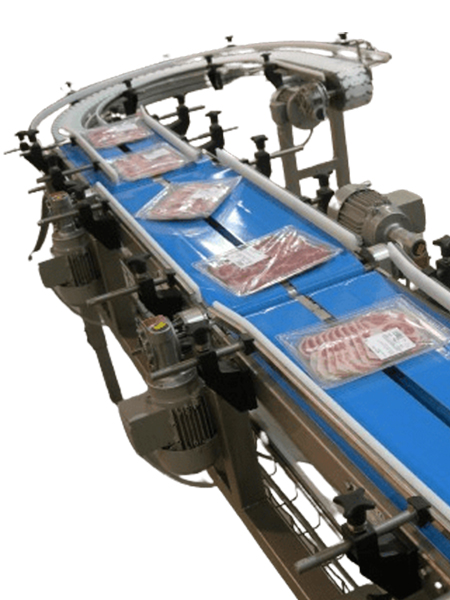
Product handling
Between primary and secondary packaging it is quite common to find tray merging devices at the exit of thermoforming and traysealing machines, followed by product handling devices such as rotation or tilting, often required before marking or labelling systems.
Mergers
Dividers
Product handling
Case packer
Semi-automatic cashing machine
The production rates of these lines are often relatively low, which is why it is still quite common to see manual casing and palletizing.
In the fastest lines, however, it is limited to the case packers. The only exception is some lines that offer sliced snacks and in which it is likely to find a packaging machine in display in addition to the case packer.

Sorter and ARB devices

Low pressure accumulation
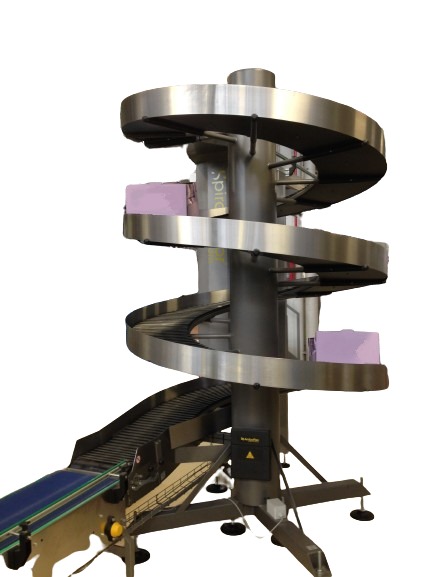
Spiralveyor
As previously mentioned, the use of manual palletizing is frequent. However, in cases of high production, the considerations for box lines adopted in other sectors remain applicable: roller belts or friction roller conveyors are used for accumulation, and activated roller belts for sorting and layer formation operations.
There is no shortage, of course, of the proverbial spirals to free up floor space and feed the palletizers from above.
In this situation, we can add semi-automatic palletizers with Cobots to our portfolio.
Sorter
ARB devices
Low pressure accumulation
Spiralveyor