Chocolate production presents an initial process stage common to virtually all types of finished products, from classic bars, through so-called hollow figures (Easter eggs and rabbits for example) to the most elaborate pralines.
The molding stage is probably the most fascinating one, where the industrialization of processes shows the most creative solutions needed to replicate the best handcrafted products.
Molding is characterized by products traveling inside particular molds and trays, so there are no particular differences between one product and another in handling technology.
Things change dramatically when it comes to the product packaging stage, where the chocolate is removed from the molds, in jargon "unmolded."
Here, depending on the type of product and packaging, it can be transferred either directly onto conveyor belts or onto trays called counter-plates or counter-molds, to go to feed the primary packaging machines.
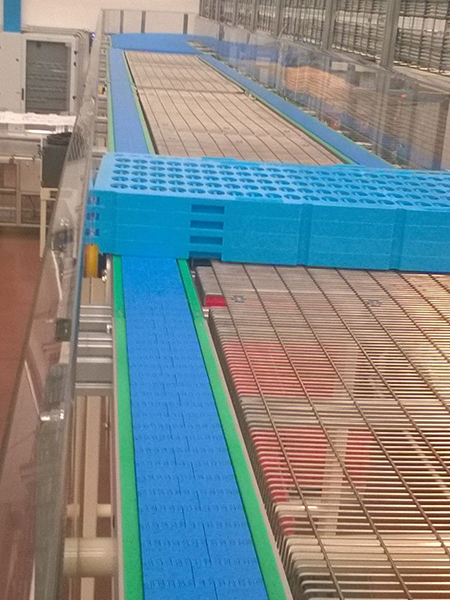
Countermoulds lines
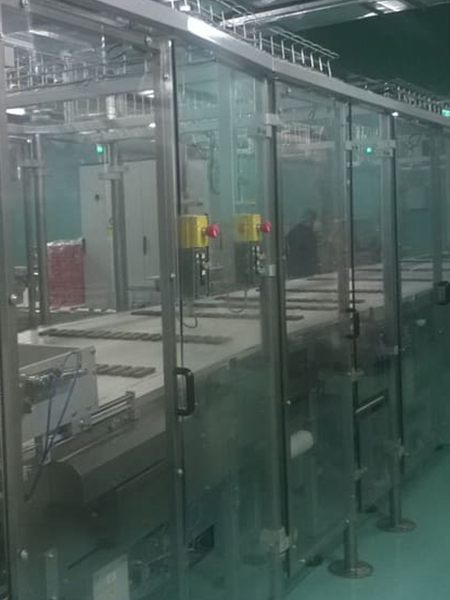
Row extraction lines
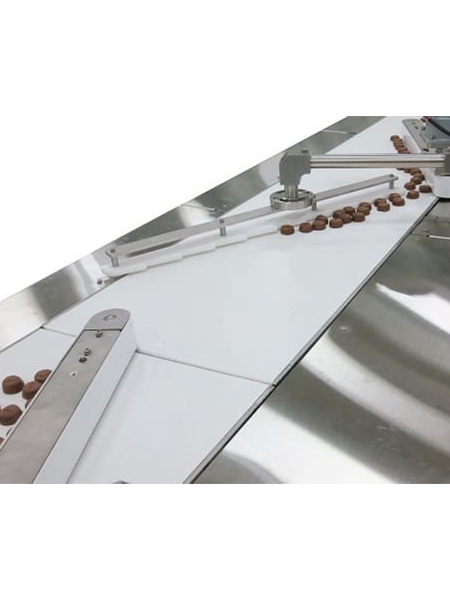
Chicane aligners
- For hollow eggs or elaborate or delicate pralines, the product remains on the counter-moulds until it is loaded onto the packaging machine, usually by pick and place.
- For small flat-bottomed chocolates, belt conveyors with a chicane system are usually used to align the product being loaded to the different wrapping machines.
- For chocolate bars and bars usually use the classic row feeding system that can load both wrapping machines and flowpacks.
Countermoulds lines Row extraction lines Chicane aligners
Flowpack
Wrapping machines
Primary packaging machines for chocolate are basically of two types:
- wrapping machines
- flowpack machines.
Hollow products and pralines are often placed directly inside acetate trays to hold them in place during linkage with secondary packaging.
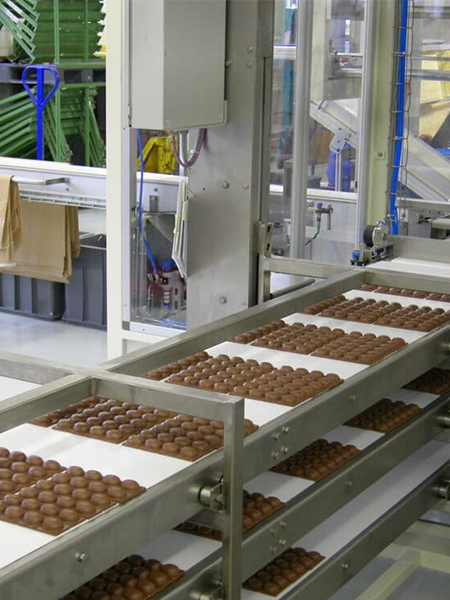
Buffer
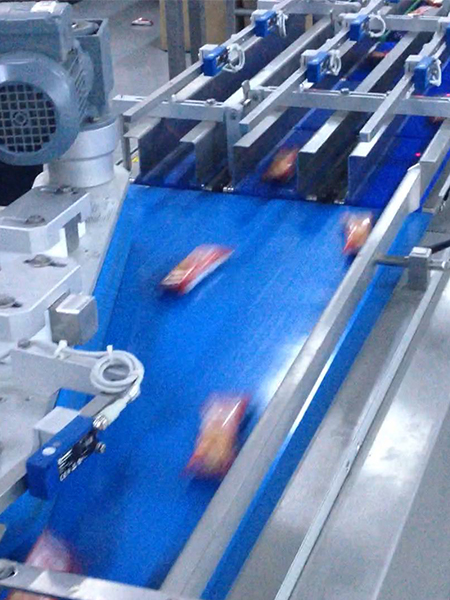
Mergers
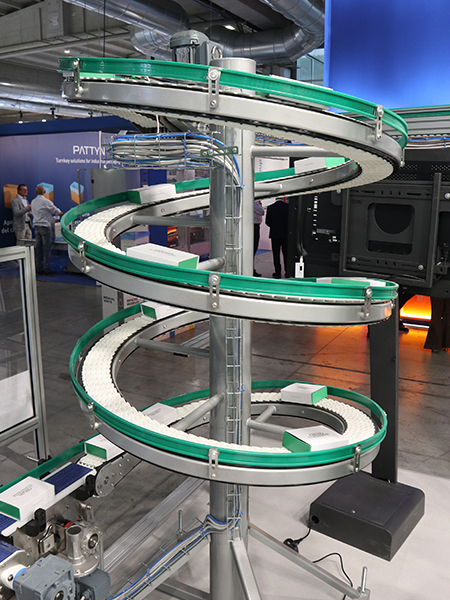
SVn-Bare light spirals
Bars and bars are typically placed in a pouch or directly into a cardboard box.
In most cases the flow of wrappers is reunified to feed fewer wrappers or casers.
It is quite common to include LIFO accumulation systems in this part of the line, and another popular trend in recent years is to free up floor space by using lightweight spirals to make the connection with the secondary machines overhead.
Buffer
Mergers
SVn-Bare light spirals
Cartoning machine
Case packer
The sequence involves cartoning or display machine followed by casing machine in the case of tablets and also pralines.
Hollow, larger products see both functions unified in the same machine, very often a wrap around, so the display itself becomes the packaging useful for shipping, especially in recent years when the push to reduce the amount of packaging material is very strong.

Sorter and ARB devices

Low pressure accumulation
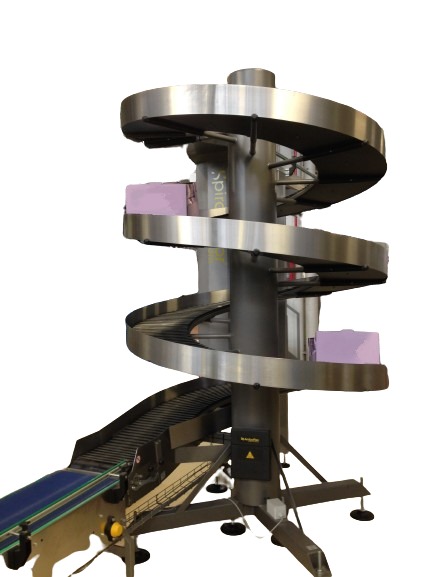
Spiralveyor
Moving towards the end of the line it is possible to encounter buffers again, but given the level of investment it is more likely that the machines used for the bare product will also compensate for the stops from the secondary forward.
Finally, the box conveyors and palletiser feeders see the usual technologies applied, from embedded roller belts or friction roller conveyors for accumulation sections to activated roller belts for sorting and layer formation.
There are, of course, the proverbial spirals to free up floor space and feed the palletisers from above.
Sorter
ARB devices
Low pressure accumulation
Spiralveyor