The packaging process in the cosmetics industry is a very special niche; marketing requirements influence the choice of packaging more than in any other sector.
The variety of shapes and sizes lead to the logical choice of using SKUs virtually all along the line that are typically called PUCK.
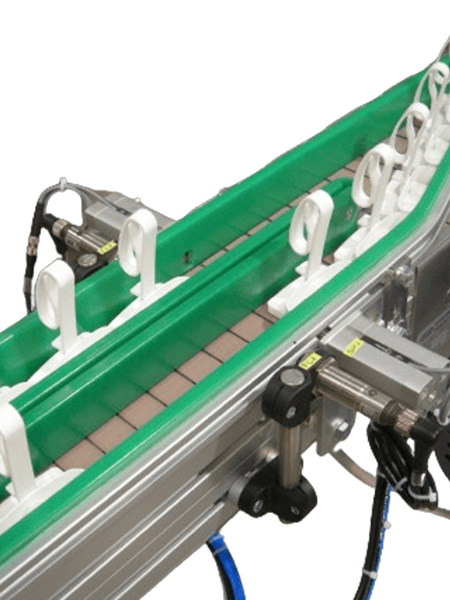
Free pallet lines
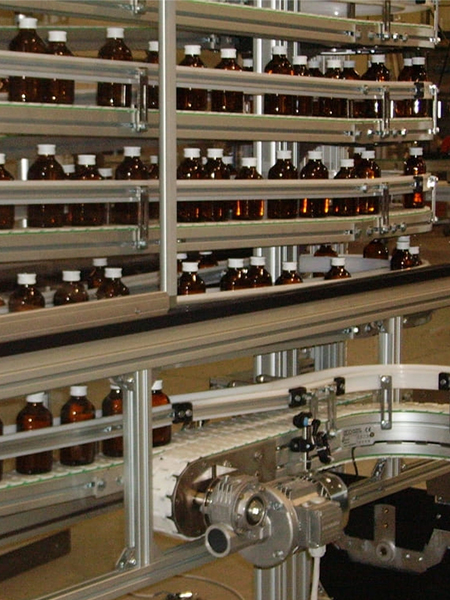
BAT Buffer
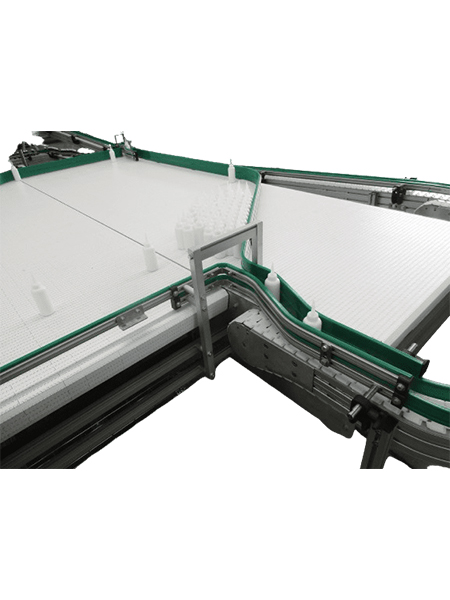
Recirculating tables
Another advantage is that there are no format changes other than that of the PUCKs themselves on the line and this allows for the easy integration of accumulation systems, typically spiral like the BAT-Buffer, or other merging and sorting devices if required by the process.
Applications for cylindrical products, such as spray cans, are an exception: in these cases, Table Top conveyors remain the preferred option. However, for accumulation requirements, a further alternative is introduced: horizontal recirculation tables.
The floor space required is certainly greater than a BAT-Buffer, but the economic advantage can be attractive.
Free pallet lines BAT Buffer Recirculating tables
Cartoners
Traysealers
Of course, the aesthetic factor plays a key role in this market; therefore, it is quite common to find cases and displays as secondary packaging, especially for products with higher added value.
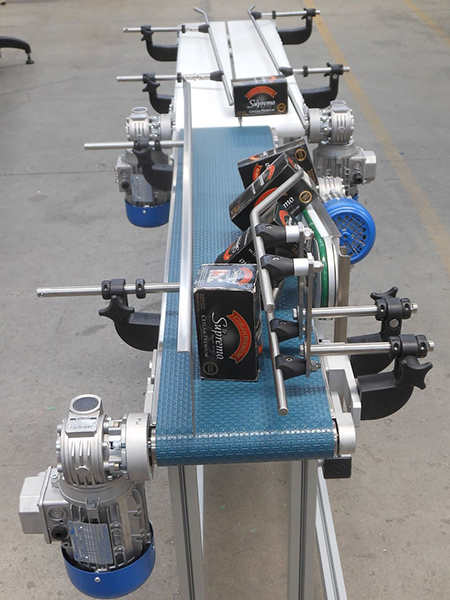
Product Handling
The most typical devices found at this stage are product handling devices, often required by a case packer or shrinkwrapper.
Product Handling
Case packer
Overwrapper
Case packers and shrink wrappers are both good and present solutions, in the case of particularly large products (typically shampoo or similar) it is also possible that the secondary is not present and these machines are fed directly from the primary.

Sorter and ARB devices

Low pressure accumulation
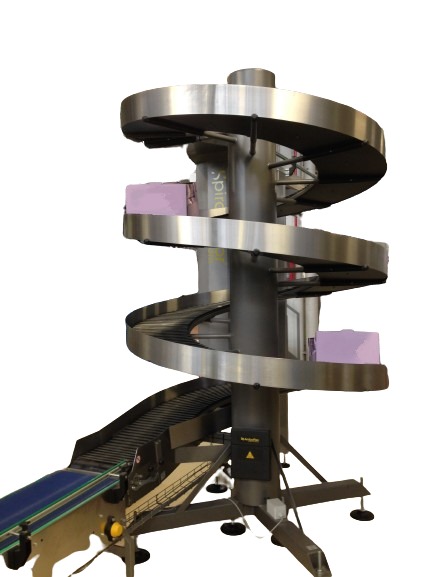
Spiralveyor
Moving towards the end of the line it is possible to encounter buffers again, but given the level of investment it is more likely that the machines used for the bare product will also compensate for the stops from the secondary forward.
Finally, the box conveyors and palletiser feeders see the usual technologies applied, from embedded roller belts or friction roller conveyors for accumulation sections to activated roller belts for sorting and layer formation.
There are, of course, the proverbial spirals to free up floor space and feed the palletisers from above.
Sorter
ARB devices
Low pressure accumulation
Spiralveyor
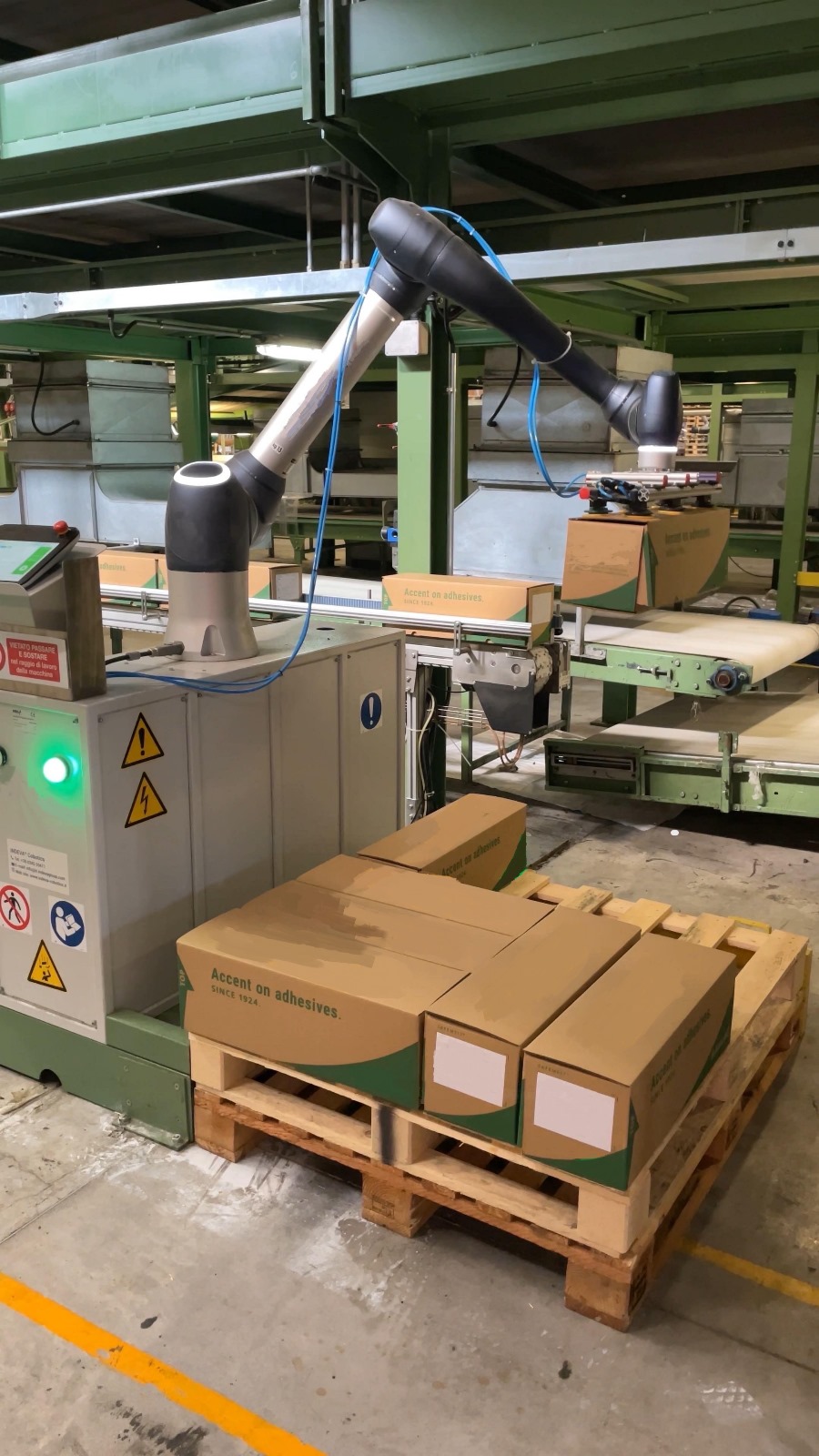
Cobot palletisers
Once we get to the corrugated box or tray level, a typical unit for pallet shipping, the solutions revert to those common to all markets: wide-chain, low-friction conveyors, friction roller conveyors, and Intralox ARB systems for package distribution and feeding to the palletizer.
For smaller and slower lines, we can add semi-automatic palletizers with Cobots to our portfolio.
Cobot palletisers